Une remarque d’une éducatrice en crèche m’a fait me poser la question suivante : faut-il toujours mesurer avant d’agir ? Dans ce cas, mon garçon paraissait fiévreux. Cependant elle me soutenait qu’il ne l’était pas, car elle n’avait pas pris sa température. Qui de l’oeuf ou de la poule? Je vous propose de réfléchir à la mesure et à la mettre en perspective avec le savoir-faire et les connaissances du personnel opérant les systèmes.
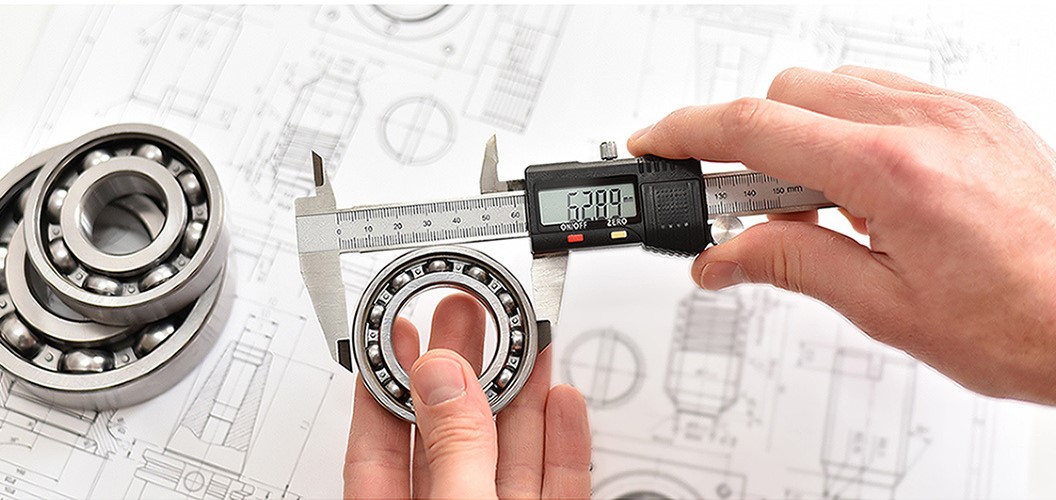
On ne peut pas améliorer ce qui ne peut pas être mesuré
Une des bases de l’excellence opérationnelle est que l’on ne peut améliorer que ce qui peut être mesuré. C’est vrai : comment connaitre la progression, si l’état initial, la situation actuelle et la cible ne sont pas connus ? Même sur des processus virtuels ou numériques, et donc moins mesurables, il y a toujours des chiffres pour mesurer la performance. Pensez au taux d’absentéisme, au score de satisfaction de la clientèle, au temps d’indisponibilité ou de livraison en retard…
Les nombres nous aident à appréhender des ensembles. Les données sont objectives. Elles simplifient la comparaison et la compréhension. Les mots apportent de la nuance et de la subtilité, mais les chiffres sont un facteur déterminant pour se faire une image mentale. Comparez : « Elle vit dans un grand manoir. » et « Elle vit dans un manoir de 300m2. », si « manoir » aide à imaginer le style, c’est bien la superficie qui donne la mesure de la grandeur.
Il en va de même dans le monde professionnel. Mon ordinateur est lent. C’est un fait, je peux faire les mises à jour, et continuer de constater qu’il est lent. Faute de données, je ne peux pas savoir si la solution apportée a eu un impact sur le temps d’ouverture d’une application.
Les situations dans lesquelles on mesure AVANT d’agir
Si vous voulez améliorer quelque chose, la première étape consiste à mesurer la situation actuelle. Vous établirez ensuite des cibles et un plan d’action. Vous mesurerez l’amélioration du processus, tout en corrigeant le plan d’action au fur et à mesure selon les besoins. C’est la fameuse roue de Deming, ou PDCA.
C’est sur ce principe que repose la quantification de soi, ou l’automesure connectée. En mesurant le nombre de pas quotidien, vous pouvez décider des actions à prendre pour atteindre vos objectifs.
Une fois que votre mesure est en place, vous pouvez vous assurer de sa performance. La méthodologie Six Sigma se base sur l’observation en continu pour prédire les déviations du processus et éviter l’apparition de défauts.
Prenons un exemple : vous voulez faire 1500 pas par jour. Si vous observez une variation importante d’un jour à l’autre, c’est que vous perdez la maitrise (stabilité) de votre processus. Même si vous êtes à l’intérieur de votre plage acceptable, vos actions apportent des résultats qui ne sont pas statistiquement fiables.
Dans un centre d’appel, si le temps moyen de traitement est de 122 secondes +/- 14 secondes, vous pouvez savoir que quelque chose ne va pas en observant les variations. Si vous notez que les temps se mettent à augmenter progressivement, vous pouvez agir, avant qu’ils ne dépassent votre limite acceptable. C’est l’intérêt de la démarche Six Sigma.
D’une façon plus générale, quand vous voulez avoir une vue d’ensemble ou mesurer des progrès, que vous souhaitez mettre en place des actions, il est préférable de commencer par mesurer.
Les situations dans lesquelles on mesure APRÈS
En cas d’urgence, il faut agir. Les premiers secours commencent par poser des gestes. Toutefois, ils passent rapidement à la mesure. Ils ont d’ailleurs une panoplie de mesures rapides, qui leur facilite l’évaluation de leur patiente. Les secouristes n’attendent pas d’avoir un bilan complet pour intervenir, mais utilisent des données, parfois qualitatives. Il est évident qu’elles ne travaillent pas en aveugle. Il est impossible de fonctionner sans information. Et pourtant, plusieurs entreprises ne connaissent pas leurs opérations. Elles ne mesurent pas leur performance et réagissent après qu’un problème se soit aggravé.
Dans le pire des cas, le problème est signalé par une cliente. C’est elle qui constate le défaut et nous en fait part. Il se peut qu’il y ait beaucoup à rattraper. Il existe plusieurs techniques de résolution de problèmes. Elles s’appuient sur la mesure, car vous ne pourrez confirmer vos hypothèses et résoudre le problème qu’en mesurant.
Il en va de même pour la prévention : vous n’avez peut-être pas besoin d’avoir une mesure avec un chiffre précis ou un tableau de bord complet pour commencer à agir. Vos équipes connaissent leurs outils et leurs opérations. Même si elles manquent de précision, les informations qu’ils vous communiquent sont importantes.
Écouter la première ligne
Dans l’idéal, les opérations s’aperçoivent d’une déviation au moment où elle se produit et peuvent la signaler. En principe, il faudrait arrêter la production (jidoka, arrêt au premier défaut) et résoudre le problème avant de poursuivre. Dans les faits, c’est assez différent. Trop souvent, le personnel de première ligne n’est pas pris au sérieux lorsqu’il remonte un problème. Il est ignoré, ou pour que le problème soit pris en compte, une personne extérieure vient mesurer et confirmer le problème (et son ampleur).
Si vous voulez gagner du temps et être performant, vous devez faire confiance à vos équipes de première ligne. Elles connaissent leurs opérations mieux que tout le reste de l’organisation. Par conséquent, si elles pensent qu’il y a un problème, vous devriez intervenir rapidement pour corriger la situation. Vous pourriez ensuite mesurer si le correctif a fait effet. Et pourquoi pas, mettre en place une mesure permanente si le problème est récurrent.
Et vous, comment prenez-vous en considération les commentaires de vos équipes de première ligne ? Sont-elles les expertes de vos processus ?