Dans l’industrie, une méthode très utilisée est la Théorie des Contraintes, parfois sans être nommée. Cette théorie aide à diriger les efforts au bon endroit, pour atteindre le maximum de résultats. Dans cet article, je vais commencer par expliquer la TOC (de l’anglais Theory Of Constraints), puis je vous donnerai des pistes pour l’utiliser au quotidien.
La théorie des contraintes améliore la performance de l’ensemble de la chaine de valeur. Voici 5 étapes à retenir pour l’appliquer. Identifier le(s) goulot(s) du système, décider comment mieux exploiter ces équipements, s’assurer que les nouvelles règles de fonctionnement sont appliquées, élever le(s) goulot(s) du système, au besoin, recommencer.
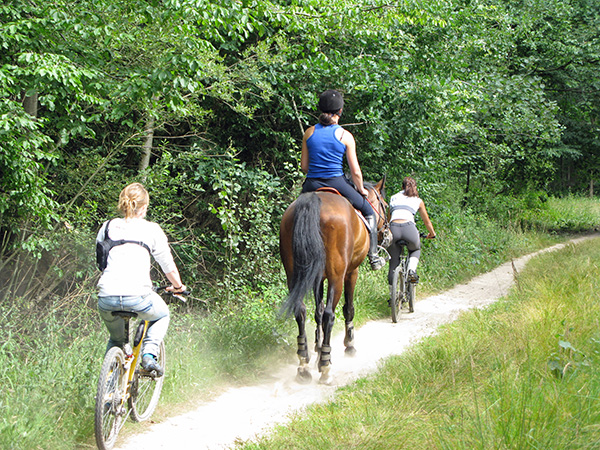
Principe de la Théorie des Contraintes
Puisque la force d’une chaine est déterminée par le maillon le plus faible, la première étape pour améliorer une organisation doit être d’identifier le maillon le plus faible.
Eliyahu M. Goldratt (1947 – 2011), Expert en gestion d’entreprise Israélien
Auteur de Le But : un processus de progrès permanent
Le rythme de la chaine de production est conditionné par celui de l’équipement le plus lent. La théorie des contraintes aide à identifier cet équipement. En élevant la contrainte du système, vous optimisez votre production.
Dans son ouvrage, Goldratt donne plusieurs exemples pour illustrer la Théorie des Contraintes. Outre la chaine en acier, et son maillon le plus faible, la troupe de scouts en forêt m’a beaucoup marquée.
En effet, même si certains jeunes sont plus rapides, la troupe de scouts n’arrivera au campement, que lorsque tous les scouts seront arrivés. Même s’ils ne sont pas physiquement reliés entre eux, c’est le plus lent qui dicte le rythme.
La performance de la troupe dépend de l’utilisation adéquate des ressources. Si le plus lent porte le sac le plus lourd, il sera encore plus lent. S’il doit aller au rythme des plus rapides, il va « surchauffer ». Un point de côté ou un essoufflement ralentiront encore plus le groupe.
En obligeant tout le monde à se caler sur son rythme, on préserve les ressources. Il est alors envisageable de porter son sac par exemple, pour accélérer son rythme et celui de l’équipe.
Le rythme de la chaine de production, son takt time, est conditionné par celui de l’équipement le plus lent.
Comment identifier le goulot
Communément appelé goulot, l’équipement contraignant est en général facile à identifier. Lors d’un Gemba, vous verrez vite où se situent les stocks accumulés. Prenez le temps de bien observer la situation, car ce n’est pas toujours aussi évident. Souvenez-vous de la fable du lièvre et la tortue. Un équipement plus rapide peut inciter ses opératrices à prendre des pauses ou aller aider ailleurs. Le stock s’accumule alors à l’entrée de l’équipement, qui n’est pas goulot pour autant.
Vous pouvez vous aider d’une cartographie de type VSM (Value Stream Mapping), avec le temps de passage sur chaque équipement. Vous pouvez aussi questionner les opératrices, qui sont souvent très au fait des goulots de production. Les gammes opératoires peuvent également vous guider. Au final, ce qui est important c’est que vous soyez certain⸱e d’adresser le (ou les) équipement(s) qui génèrent les contraintes. Les maillons faibles de votre usine en quelque sorte.
Comment supprimer le goulot
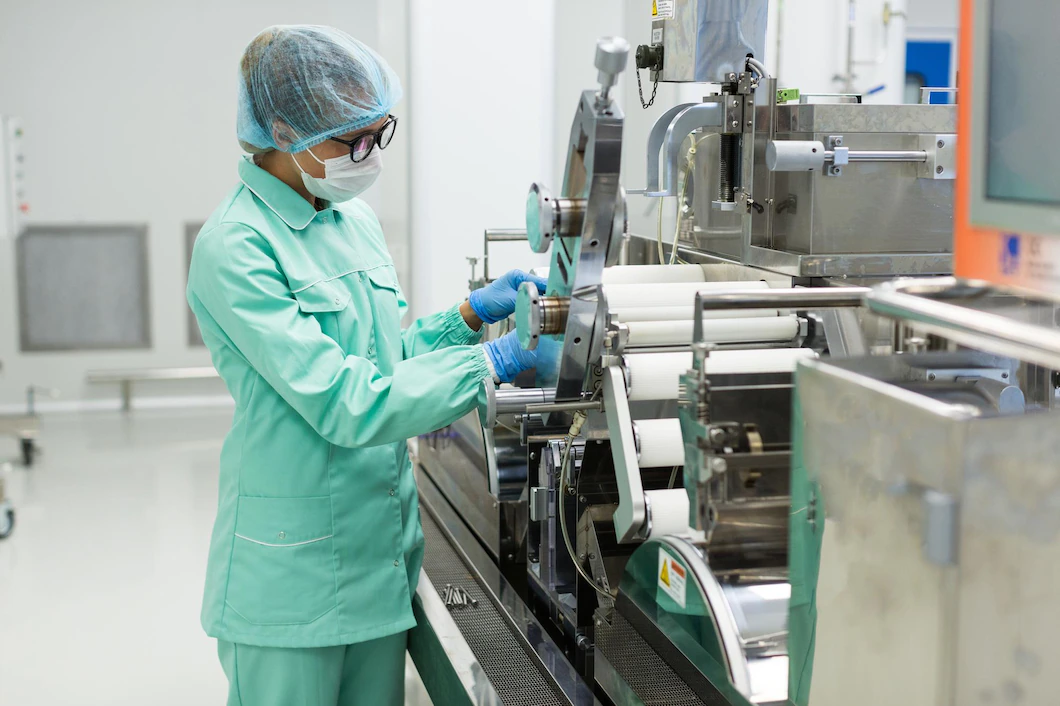
Ensuite, c’est le temps de l’observation. Vous devez déterminer pourquoi cet équipement cause un goulot. Il faut réaliser un diagnostic précis afin d’adresser les causes racines. En utilisant les 5 pourquoi à plusieurs reprises, vous allez dresser un arbre des causes. Vous pourrez alors décider le bon plan d’action.
Voici quelques exemples de causes fréquentes :
- L’équipement n’est pas fiable. L’opératrice doit fréquemment faire des réglages. Elle vérifie beaucoup les pièces. Elle ajuste la machine en cours de production. Ou encore elle reprend certaines pièces deux fois pour qu’elles soient bonnes. Dans cette situation, c’est la méthodologie Six Sigma qui va vous aider à réduire la variabilité dans la production.
- L’équipement est long à préparer pour chaque nouvelle série. Vous travaillez avec de plus petites séries, mais cet équipement prend du temps à régler. Vous avez augmenté les tailles de lots, mais ça ne répond pas à la demande. Dans ce cas, c’est le SMED qui va aider à réduire le temps requis pour passer d’un type de pièce à un autre.
- Le poste de travail est globalement désorganisé. L’opératrice fait beaucoup de manipulations. Elle déplace les pièces plusieurs fois, fait de nombreux aller-retour. Dans ce cas, il faudra commencer par un diagramme spaghetti. Vous pourrez ensuite améliorer le flux et surtout l’ergonomie du poste. Vous allez peut-être réorganiser les équipes ou la gestion des priorités.
Dans tous les cas, vous n’oublierez d’utiliser les 5S pour finaliser votre chantier d’amélioration. C’est en général avec une approche Kaikaku que l’on corrige le goulot. Une équipe travaille pendant quelques jours pour venir à bout du problème.