In the age of cost-cutting and musculoskeletal disorders, robots seem well placed to help us perform a number of repetitive tasks.
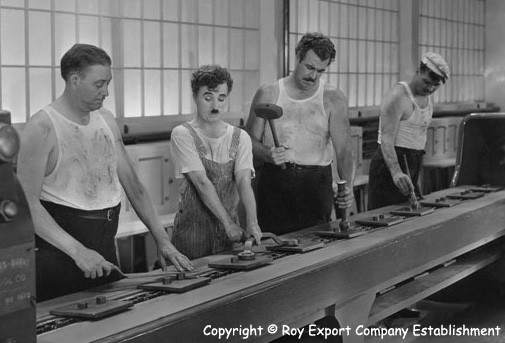
In May 2010, I had the opportunity to visit the Centre de Robotique et Vision Industrielle (CRVI), based in the Cégep de Lévis-Lauzon, Canada. In May 2022, I participated in a demonstration of Industry 4.0 solutions by Callaghan Innovation, New Zealand’s innovation agency. I was able to see and share with experts the latest technologies in the field of robotics.
You will find on their website all the information and details about the support they provide to organizations. Their role is to help manufacturing companies to use the latest technologies. Both New Zealand and Quebec are facing labour shortages. Technology improves productivity in many ways. Thanks to government programs, organizations can benefit from it at a lower cost. There are similar programs and support in all countries.
The four industrial revolutions
Robots have been used in industry since the third industrial revolution. In machining, welding, assembly, they no longer need to demonstrate their superiority over humans to perform repetitive, painful or dangerous tasks. Without lungs and muscles fearing for their health, they know how to replace humans in many cases. They are therefore particularly effective for simple and standardized actions.
Their programming did not allow them to adapt to a process variability until now. If the operator did not place the parts to be welded or machined in a very precise position, the robot could not perform its task properly. This constraint required the installation of costly templates or jigs. It has long limited their development by the low return on investment.
Robotic technologies of Industry 4.0
Several technologies improve these aspects and increase the use of robots in factories. For example: vision, pressure sensors and artificial intelligence.
These technologies give the robot sight and touch as well as a small capacity to learn. Intelligence remains programmed by human, but the robot is “capable” of making decisions and adapting to a process or product with small variations.
To understand what these technologies can bring, nothing better than some examples and a video.
The contribution of vision
The robot is equipped with one or more 2D or 3D cameras. These cameras take pictures of the area where the robot will intervene. A program analyzes the image. The robot’s programming then permanently shifts the robot’s position according to the information received.
In the example below, you can see a classic: Handling parts on a treadmill to arrange them properly. This is a FANUC robot. The vision is used in this case to identify the position of the piece to be taken.
Another use developed by the CRVI is the welding/machining trajectory correction. One or more cameras capture the image of the work piece. The robot is programmed in relative: it knows the trajectory to be accomplished. The image taken allows to give the starting location, and to calculate the precise displacement of the robot. To ensure quality, it is possible to define a trajectory change tolerance. If the position of the parts is too staggered with the “standard” position, the robot stops its action and the operator must intervene.
The gain for the company : less complex and less costly templates, reduced operating time to set up the parts (less precision required).
The contribution of pressure sensors
The sensor can measure forces according to the 3 axes (X, Y and Z) as well as the moments on these 3 axes. This ability to “feel” force can be used in many applications, especially for humanoid robots. On the industrial side, this technology can be used to:
- Guarantee the assembly of one part in another. The robot knows the position of the piece to be assembled and the path to be carried out. If, during the course of his journey, he receives incompatible information (e.g. misaligned or poorly calibrated part), he corrects his trajectory. If the part does not match the assembly tolerances, it will stop its action. The operator is responsible for checking the quality of the parts.
- Standardize a product: If two pieces are to be assembled with a force of 10 pounds, the robot will adapt according to the hardness of the materials and their variability. In this way, the assembly will always have a strength of 10 pounds. It modulates the pressure applied according to the information returned by its sensor.
The gain for the company : the possibility of automating and standardizing a process, a result with a constant quality level.
The contribution of artificial intelligence
It is mainly in the field of quality control that artificial intelligence is used in Industry 4.0. Indeed, some processes require 100% quality control, such as in the food and medical industries.
The systems are very difficult to program, with machine learning, the team can train the robot and teach it. After a training period, the machine outperforms humans. The number of errors decreases, until the robot knows when to ask for validation.
Artificial intelligence can also help maintenance teams perform preventive maintenance, by learning from breakdowns. The causes are often multiple, and artificial intelligence can test several factors, such as temperature, humidity, type of part produced, in order to predict the next required breakdowns or adjustments.
The gain for the company: Make the best use of the teams, while ensuring the repeatability of the processes. Document and understand the problems to better solve them.