SMED means Single Minute Exchange of Die. This is not a one-minute exchange of die. Indeed, « single minute » refers to « single digit minute ». So a change that can be done in 1 to 9 minutes.
SMED is a proven tool in the industry. It is simple to implement and provides savings of 30 to 70% on the time required to change tools or series. I explain how to use it to improve your performance in services and software development.
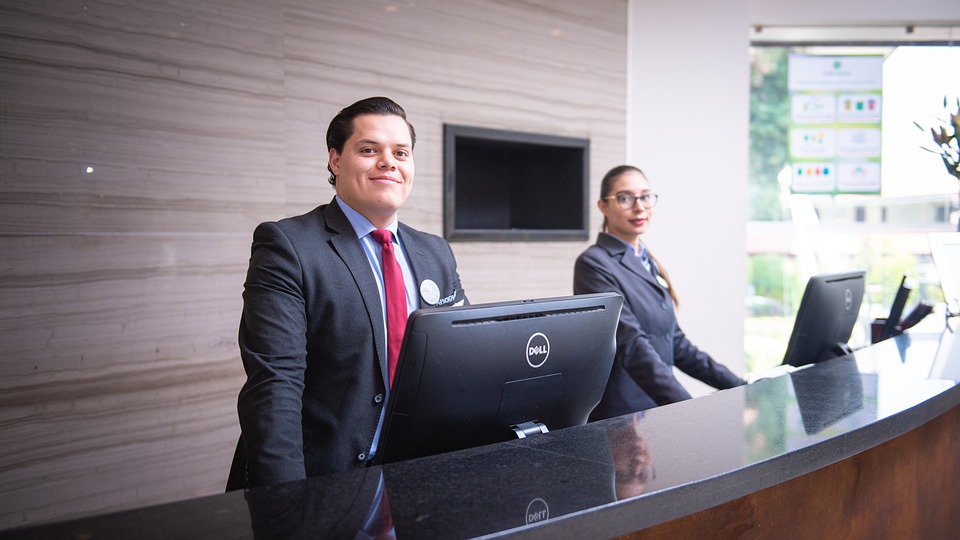
The origins of SMED
Let’s give Shigeo Shingo credit for his creation: this tool was formalized at Toyota. It addresses the time required to change a tool. Indeed, it aims at reducing the batch sizes and increasing the flexibility of the company.
The original problem is the following: on a sheet metal press, a tool forms the doors of a vehicle model. Since it takes several hours of work and adjustments to change the tool before producing the doors for another vehicle, the batch sizes were increased. The company manufactures the same part for several days. This way, it creates an important stock. It then changes tools and starts another model. The company wants to maximize its profitability. Assuming that the parts are good, its production time is thus optimized.
This production organization has two problems. On the one hand, the creation of large intermediate stocks, with the costs that this entails (immobilization, storage space…). On the other hand, the risk of defects on a large number of parts. If the operator detects a defect during assembly, several days of production will have to be corrected or destroyed.
With this in mind, Shigeo Shingo formalized this rapid tool exchange approach.
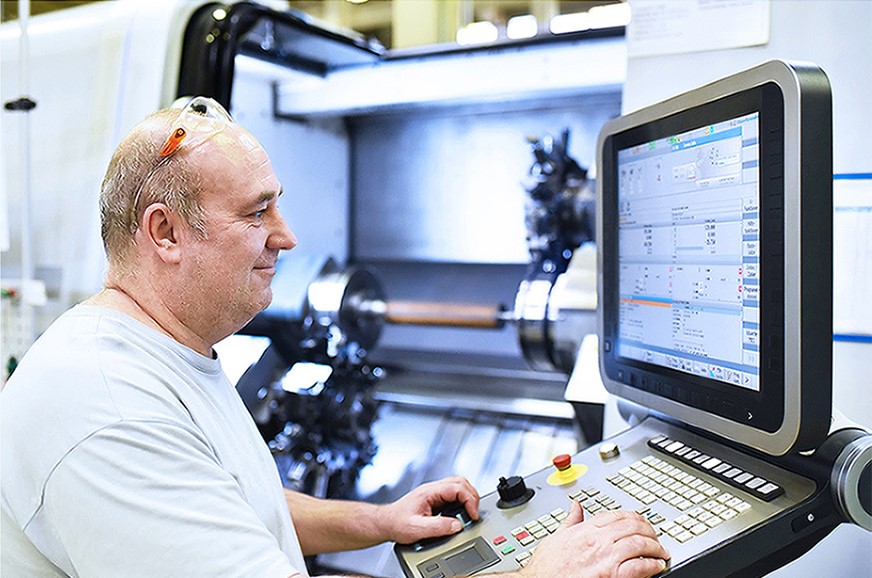
What is SMED?
The tool change is defined as the time between the production of the last good part of series A and the first good part of series B.
In the industry, this time therefore includes:
- Removal of the tool and raw materials,
- Cleaning of the machine or the production line,
- Setting up the new tool and raw materials,
- Adjustments and tests.
SMED workshops are usually conducted in the form of a kaikaku. The group observes several tool changes and notes all the operations performed. The group must include all people involved with the equipment in production: operations, maintenance, quality and design teams.
From the activity list, all operations are evaluated using the internal/external filter.
An internal operation requires the equipment to be shut down to be performed. An external operation is independent of the equipment.
Now is the time to make the improvement:
- Identify all the operations that can be carried out at another time: fetch a tool, prepare the raw material for the next production run, etc. These operations are called external, because they can be performed outside of the production shutdown.
- Transform internal operations (which require the equipment to be shut down) into external operations: programming of settings, etc.
- Reduce the execution time of internal operations: use of templates, production standards… During this step, the team may decide to remove some operations.
- Finally, reduce the execution time of external operations.
The use cases in the industry are numerous:
- New color on a paint line,
- Mold change on a press,
- Different publication on a high volume printer,
- New drug on a pharmaceutical line,
- Different packaging in a food factory.
Examples of SMED for manual processes
The best known example is of course the wheel change during Formula 1 races.
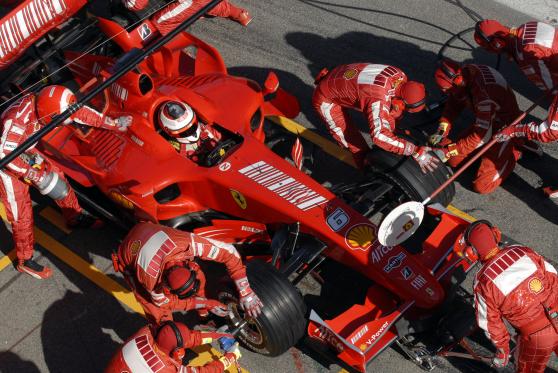
Implementation or withdrawal of a promotion in a retail shop
In this case, we will be looking to reduce the time required to put on or remove the labels marked “-20%” as well as the downtime of the computer system to make the changes.
The staff performs these operations during the closing of the store, they do not impact the customers. But the staff is paid, while no customer is present. Reducing changeover time increases the time paid to customers and therefore profits. Observing operations will help determine which operations can be performed at other times and optimize work times.
In a hospital
Here are two examples:
- Changing patients in the operating room
- The release of a patient room
In both cases, the team completes a series of actions before moving on to the next. The shorter the downtime, the greater the number of patients treated. Again, the same method applies to reduce this delay and provide better service to patients.
In combination with the theory of constraints, one hospital determined that its critical resource was the surgical team. So they have two operating rooms and alternate between the two. Other teams are responsible for cleaning the room after surgery, preparing the room and the patient before the surgical team arrives.
Change between two clients in the customer service
While the person is finalizing the file, he or she is not present for another client. If the processing time after seeing a client is long, more staff will be needed to handle more clients. Reducing the processing time between customers improves the quality of service.
An easy technique to turn internal operations into external operations is to move file closing tasks to the end of the day or to times when there are no customers. The operation is external, since it is faster to move from one customer to another. However, if there is no off-peak period during the day, the operation only improves service quality, with no impact on financial performance, because these activities will be carried out after the closure. So it’s important to think about your performance model before doing SMED.
Update or migrate a database, an application or a website
In these situations, the goal is to reduce downtime and system unavailability for users. The same principles and methodology apply.
- Determine which external operations can be performed before or after the update. There are no changes to be made, except for the time of execution of the task.
- Transform internal operations into external operations. Adjustments or changes in processes will be required to achieve this.
- Reduce the time required for internal operations. By optimizing checklists for example.
- Reduce the time required for external operations. If the system is available to users, it is still time that can be optimized.