Gemba is the terrain where value is created where field problems are dealt with. You have to go see with your own eyes , question the teams in the field (ask why) and value the ideas and proposals that are made (show respect).
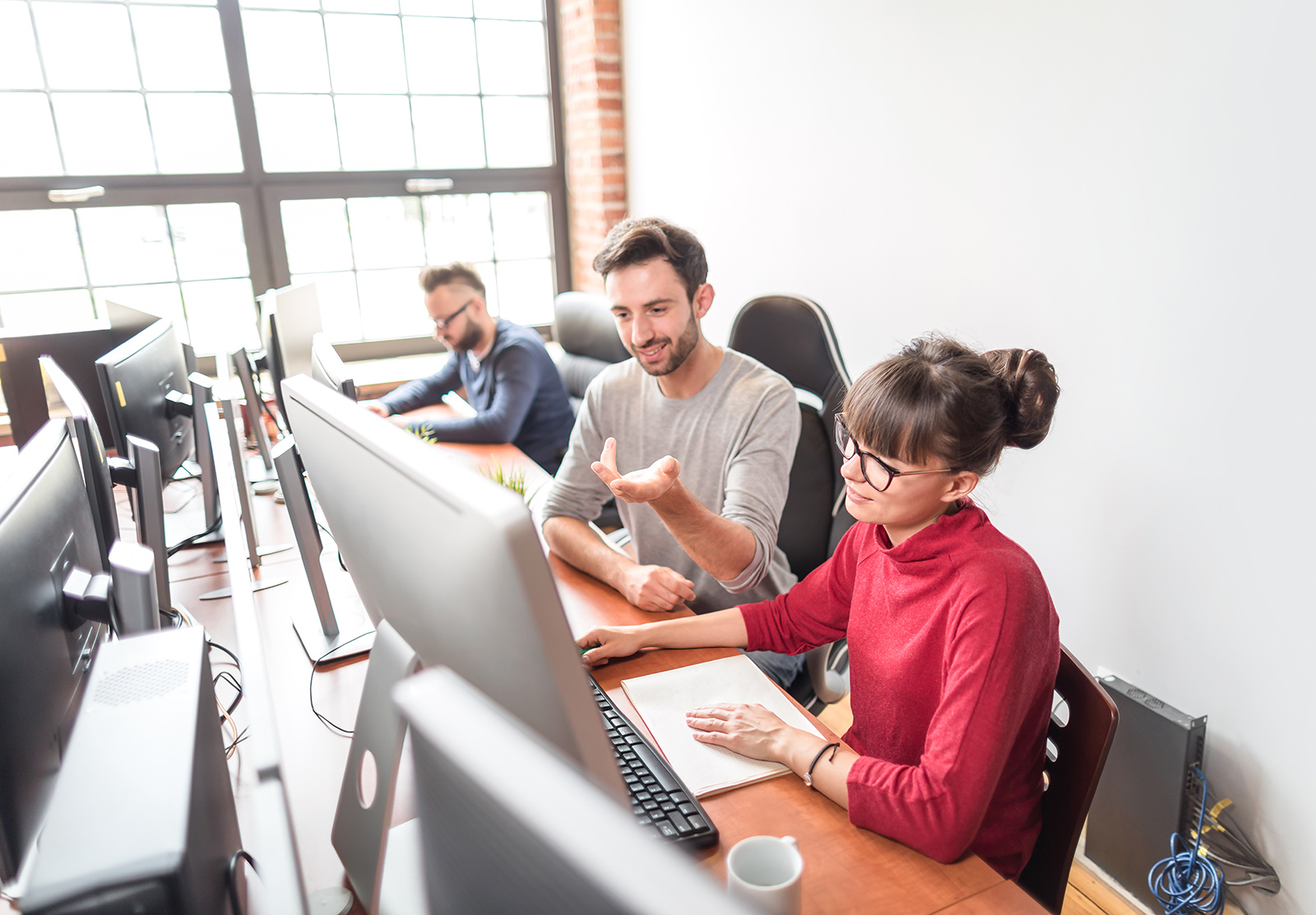
Go observe, ask why, show respect
Fujio Cho (born in 1938), Toyota Motor Corporation honorary Chairman
Gemba, a word that “sounds” good
The process is simple. The principle is also simple to understand. However, implementing it requires patience, humility and attention.
It could become an overused buzz word. But it is more important to understand the concept and apply it as often as possible.
This article deciphers the notion of Gemba and what revolves around it: gemba walk, gembutsu.
What is Gemba?
Gemba is the founding principle of operational excellence. This is why it is useful to improve a process, to develop a functionality of a software or to put in production a new product or service. All Agile, Lean, Six Sigma methodologies are based on the Gemba concept, without naming it.
The Japanese term Gemba refers to “where the action takes place”. It could be translated as the field. In a factory, we obviously think of the production line, where the manufacturing activities take place. But the offices, where the purchasing, planning, design, sales are done are also Gemba. Finally, in the Agile world, Gemba is where the software is developed and tested.
By extension, the Gemba designates all places where value is created in the organization. Value is what the customer buys: the quality of the product or service, for example.
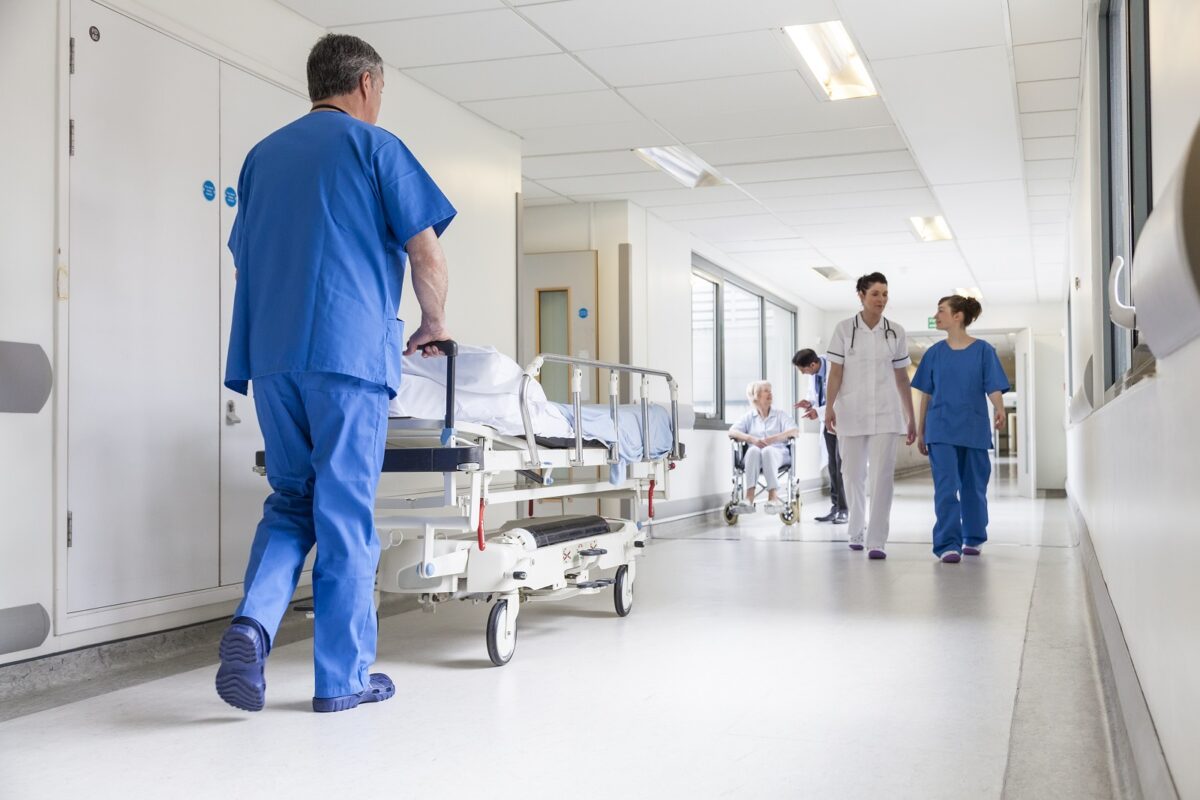
Why is Gemba so important?
In my article on business models, I ask about the power given to frontline teams. The principle is to deal with problems of the field, on the field.
Foster communication with front-line teams
When the management goes on the field it clearly indicates how important it is. These are not just words and values displayed on a sign, it is a reality. In addition, teams are more comfortable in their work area. They master their environment and will exchange more easily.
One can easily imagine the shyness of an operator or a developer to talk with the general manager of her company. Especially if the discussion is about a problem and takes place in an office. Both the operator and the developer will be very uncomfortable sharing their reality.
Explore, experiment, test
On the other hand, it is always easier to explain a situation or a problem by being on the spot. A work group or a manager will save time by going to the site to understand: in addition to the verbal explanation, they will be able to see, touch, feel, test what is being talked about. The explanations and exchanges will be clearer and more productive. We are sure to understand each other. Therefore we save time for the continuation of the project or the treatment of the problem.
Finally, by talking around an equipment or a work area, creativity will be released, with the possibilities of testing and the use of the different senses. Remember that everyone is more sensitive to hearing, sight or touch. On the ground, all senses awake, everyone will make the most of his or her qualities.
When should you go on the field?
Despite overloaded schedules, it is important to visit the field as often as possible.
If you manage a team, this is an activity you should do every day. If you work in operations support, you should take the time once a year to check out what’s happening on the Gemba. I am thinking of the human resources, finance and communications teams. If you work for projects or IT, I suggest visiting four times a year, in different areas to better understand your internal customers.
Evaluate Gembustu, produced defects
Following an accident, a breakdown, a quality problem, instead of convening a meeting in a room and bringing objects / actors from the field in the room, why not go to the field? You will have the chance to see the defects produced (in Japanese: gembutsu). You will be able to see the operations working normally and ask yourself what caused the malfunction.
Be more efficient in projects
In the context of a project, it is also relevant to go to the field. In one of my mandates, I was involved in a Six Sigma project, as a representative for the plant. I was stunned to spend 8 hours working on the equipment in a meeting room. The other participants did not have the chance to see the equipment.
How can we be effective and relevant without knowing what we are talking about? By going to see the equipment in operation, we could have easily saved 4 hours of meeting time, wasted explaining and imagining what could happen if each button was pressed.
Before you buy new software for a sector, you need to know how it works. If you find that there is a lack of performance or communication, it is not the implementation of a new system that will solve the problem. Indeed, the root cause search must go through the visit on the Gemba.
The Gemba Walk
Another opportunity to visit the field is the Gemba Walk, which is a specific activity. Frontline managers should be out in the field with their teams all the time. Other members of the management team should take the time, once a day to once a week, to visit the field.
Be careful, this is not a “health” walk. At first, you can focus on a workshop, or a work area and watch the operations work for a few moments. The objective is to understand what is going on and to talk about it with the teams. Once the process is known, the observation period may be shorter and look like a factory “tour”.
If your operations are digital, you can also go to the Gemba. I explain how to walk a virtual process in another article.
When you know how everything is supposed to work, you will be able to detect malfunctions very quickly. One of the best ways to do this is to do it yourself. But this is not always possible.
- Well, what does this palette do in the middle of the way? Usually there is nothing here …
- There is a larger volume of files / parts than usual in this area …
- What does this person do with his documents / parts in this part of the factory / office? It is not in the normal process …
- It seems to me that a lot of post-its are accumulating on this tracking board…
How to go Gemba?
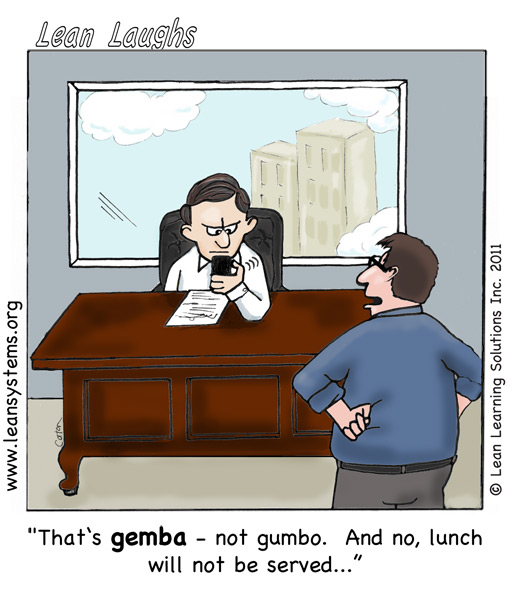
For field visits to be successful, there are some prerequisites:
Be open-minded
Even if managers know the theory and know how the organization should work, a multitude of factors disrupt this ideal operation, from the weather, to the mood of each person, to computer systems or an accident that delays a delivery. The organization constantly adapts to these factors and does not always work according to the defined rules. You should therefore keep an open mind and, before rejecting the modified way of working, ask yourself and the teams about the causes of the dysfunction.
Be a bit naive
Field expertise belongs to the people who do the work, often since many years. Their experience and knowledge are valuable and must be taken into account. They often have good ideas for improving things in their area. You need to take note of these ideas. You probably have your ideas, and maybe you have already tested them. However, you must be naive and listen to the proposals from the field. Refrain to judge hastily. You will then check the impacts on the other sectors. You can then implement them or explain to teams why they are not working for the organization.
By increasing knowledge of the organization and the impacts on other sectors, operational teams will be more relevant in their future proposals. We can also take them to do the Gemba Walk in another area.
In the industry, there is just one thing that the management team will have to be adamant about: safety. If glasses are mandatory, everyone must wear them, you must be exemplary in this area.
Have an objective
As explained above, the purpose of a field visit is to address a problem, to get a sense of the state of the business. It’s not a daily walk to chat with teams about the weather. You must know why you are going on the field. Ideally, your goal will be SMART or at least measurable.
On your next Gemba walk, try one or two things to be more relevant. You will quickly find what works best for you. The key is to be present (go see), open (ask why) and authentic (show respect).
Put yourself in a box and observe
To succeed in your Gemba, remember that you have two eyes, two ears and one mouth… So you should speak less than 20% of your time in Gemba. If you are speaking, it is to ask questions and clarify the action or why of the action.
Under no circumstances during a Gemba should you comment, or worse, criticize, what the observed person is doing. On the one hand, you do not have all the information to understand its action, on the other hand, you would lose his confidence and will no longer be able to observe effectively.
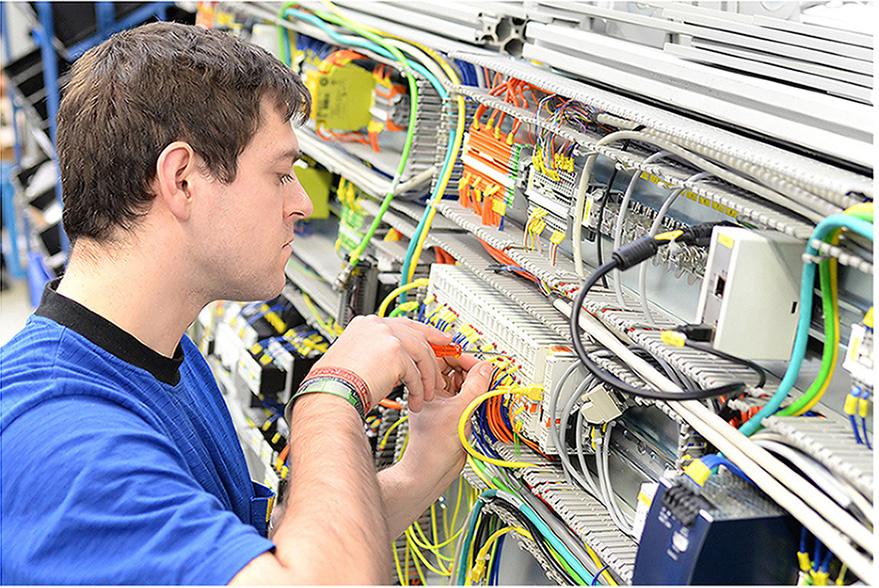
An example of a Gemba in a factory
Industrial processes can be long, both in time and space. So you will define an area and a portion of the process that you will observe. Ideally, limit yourself to a few square meters. If you can have a fixed observation post, even better.
Start by observing the flow of products: what products are they, are they varied? Where do they come from, what equipment do they pass through, what operations are performed, where are they stored, where do they go next, how often do the products arrive, are processed or leave.
Then observe the flow of people: do they follow the product, do they go back and forth, do they leave the observed area, often, for a long time, do they stay still, do they work on the product, do they check the quality, the equipment? What are their main activities, how do they feel? You can then observe their posture and the ergonomics of the workstation. Imagine the impact on the body of these actions, carried out every day for forty years.
Finally, you can listen to the noises,the machines, the vehicles, the people. What predominates? Is the atmosphere noisy, rhythmic, chaotic, serene? Do you hear noises that seem abnormal to you, where do they come from?