Dans un monde ultra-compétitif, toutes les entreprises souhaitent arriver au meilleur équilibre entre les coûts, la qualité et les délais. Dans l’industrie, la qualité à moindre coût peut au final coûter cher. C’est pourquoi le concept de poka-yoke est si souvent utilisé.
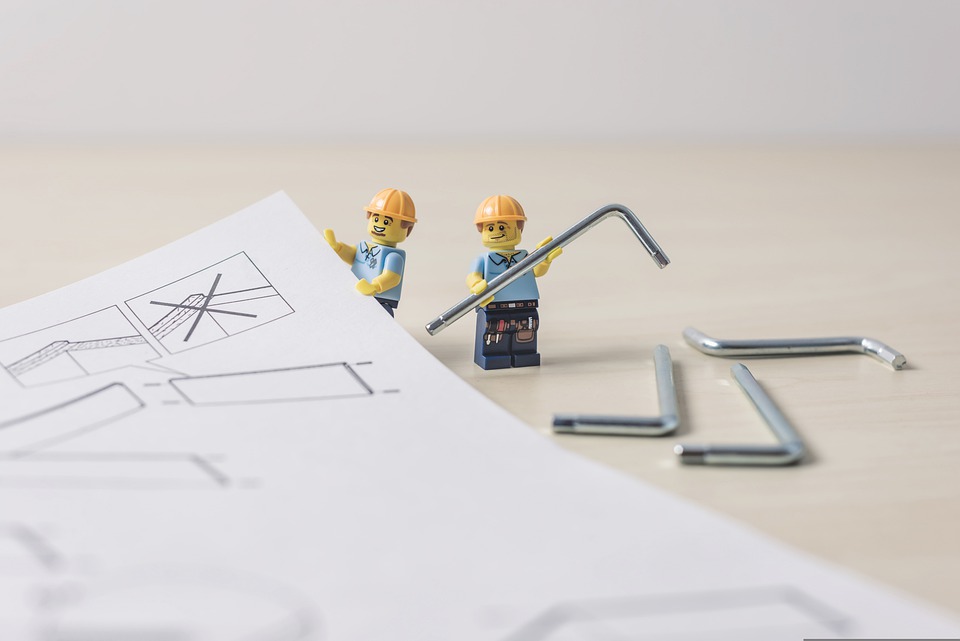
Quand l’assemblage de pièces se fait manuellement, comment garantir que l’opérateur monte toujours la bonne pièce au bon endroit ? C’est le but du détrompage, aussi appelé poka-yoke.
Le poka-yoke, ça se mange chaud ou froid?
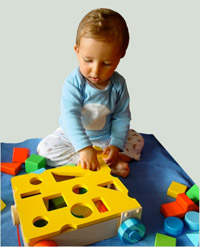
Un mot japonais pour un concept simple… Dès notre jeune âge, nous apprenons ce principe. Comme dans ce jouet, chaque pièce ne peut aller qu’à un seul endroit, le « bon ». Le poka-yoke est une méthode préventive, mise en place en amont, dans le but d’empêcher une erreur.
Les systèmes poka-yoke doivent être conçus le plus simplement possible, car ils doivent garantir que les toutes les pièces soient bonnes. Il s’agit d’un contrôle à 100%.
Si chaque pièce peut aller à un seul endroit dans un seul sens, plus besoin de vérifier que c’est bien fait.
Ce principe s’applique bien sûr à la fabrication, pour optimiser les opérations et faire bon du premier coup. Mais il est également utile pour l’utilisateur. Le détrompage aide l’utilisateur à bien utiliser le produit. Vous lui simplifiez la tâche.
Comment empêcher les utilisateurs de se tromper?
Il existe deux grandes méthodes: mécanique et visuel. Le détrompage mécanique est plus fiable que le détrompage visuel, mais plus complexe et plus dispendieux à mettre en œuvre. En général, il est utilisé pour les cas les plus critiques, où une erreur peut avoir un impact sur la sécurité des biens ou des personnes.
Dans l’industrie, le détrompage mécanique peut se faire de plusieurs façons :
- Différences de taille ou de forme
- Ajout d’une protubérance à un endroit précis
- Système de fixation positionné différemment pour chaque pièce
- Ressort ou levier activé par la pièce
Par exemple, la connexion USB est détrompée mécaniquement. Vous ne pouvez pas brancher une clé USB à l’envers ou dans un mauvais connecteur.

Les piles sont un autre exemple intéressant. Bien que la polarité soit physiquement différente, c’est en général des aides visuelles que nous trouvons dans les produits. En effet, c’est plus simple d’imprimer un symbole « plus » ou un dessin de pile que de s’assurer que la pile ne peut se mettre que dans un sens.
Par contre, les chargeurs de piles ont un détrompage mécaniques. Vous pouvez essayer, mais la pile ne peut pas se clipper et se charger à l’envers. Nous sommes exactement dans le cas ou le risque est trop grand pour détrompage visuel.
Le choix entre un poka-yoke visuel ou mécanique se fera en fonction du risque d’erreur, des impacts pour le client et du coût.
Le système de détrompage peut être placé à différentes étapes du cycle de vie du produit : lors de la conception, lors de l’industrialisation ou lors de l’amélioration du process. Il est évident qu’un produit conçu avec le système de détrompage est toujours la solution la plus efficace. Toutefois des solutions simples, telles que des gabarits (jigs) ou des codes couleurs peuvent être mis en place lors d’une démarche d’amélioration continue. En plus de l’aspect anti-erreur, ce type de systèmes diminue la charge cognitive de l’opérateur et la fatigue intellectuelle, sources de stress.