A comment from a daycare teacher made me wonder: should we always measure before we act? In this case, my boy looked feverish. However, she maintained that he was not, because she had not taken his temperature. The chicken or the egg? I suggest that you think about the measurement and put it in perspective with the expertise and knowledge of the personnel operating the systems.
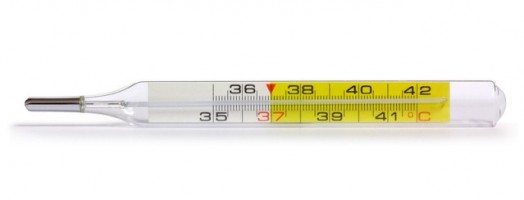
You can’t improve what you can’t measure
One of the foundations of operational excellence is that you can only improve what you can measure. It’s true: how can we know the progress, if the initial state, the current situation and the target are not known? Even on virtual or digital processes, therefore less measurable, there are always numbers to measure performance. Think of the absenteeism rate, the customer satisfaction score, the downtime or late delivery…
Numbers help us to understand sets. The data is objective. They simplify comparison and understanding. Words bring nuance and subtlety, but numbers are a key factor in forming a mental picture. Compare: “She lives in a big mansion” and “She lives in a 300m2 mansion”, if “mansion” helps to imagine the style, it is the surface that gives the measure of the size.
The same is true in the professional world. My computer is slow. It’s a fact, I can do the updates, and still find it’s slow. Due to the lack of data, I can’t know if the solution has had an impact on the opening time of an application.
Situations in which we measure BEFORE we act
If you want to improve something, the first step is to measure the current situation. You will then establish targets and an action plan. You will measure process improvement, while correcting the action plan as needed. This is the famous Deming wheel, or PDCA.
This is the principle behind the quantified self. By measuring your daily step count, you can decide what actions to take to reach your goals.
Once your measure is in place, you can ensure its performance. The Six Sigma methodology is based on continuous observation to predict process deviations and prevent defects from occurring.
Let’s take an example: you want to take 1500 steps a day. If you observe a significant variation from one day to the next, you are losing control (stability) of your process. Even if you are within your acceptable range, your actions bring results that are not statistically reliable.
In a call center, if the average processing time is 122 seconds +/- 14 seconds, you can tell something is wrong by looking at the variations. If you notice that the times start to increase gradually, you can take action, before they exceed your acceptable limit. That’s the point of the Six Sigma approach.
More generally, when you want to have an overview or measure progress, when you want to implement actions, it is better to start by measuring.
Situations in which we measure AFTER
In an emergency, action must be taken. First aid starts with gestures. However, they quickly move on to measurement. They have a range of quick measures that make it easier for them to assess their patients. Rescuers do not wait for a complete assessment before intervening, but use data, sometimes qualitative. It is obvious that they do not work blindly. It is impossible to function without information. And yet, many companies do not know their operations. They do not measure their performance and react after a problem has worsened.
In the worst case, the problem is reported by a customer. It is she who notices the defect and reports it to us. There may be a lot to catch up on. There are several problem-solving techniques. They are based on measurement, because you can only confirm your hypotheses and solve the problem by measuring.
The same is true for prevention: you may not need to have a metric with a specific number or a full dashboard to start taking action. Your teams know their tools and operations. Even if they lack precision, the information they give you is important.
Listen to the first line
Ideally, operations notice a deviation as it occurs and can report it. In principle, production should be stopped (jidoka, stop at first defect) and the problem solved before continuing. In reality, it is quite different. Too often, front-line staff are not taken seriously when they report a problem. It is ignored, or in order for the problem to be taken into account, an outside person comes to measure and confirm the problem (and its magnitude).
If you want to save time and perform well, you need to trust your frontline teams. They know their operations better than anyone else in the organization. Therefore, if they think there is a problem, you should act quickly to correct the situation. You could then measure whether the fix has taken effect. And why not, implement a permanent measure if the problem is recurrent.
What about you, how do you take feedback from your frontline teams? Are they the experts on your processes?