In manufcaturing, one methodology often used without being named in the Theory of Constraints (ToC). It targets efforts to the right place to achieve the maximum results possible. In this post, I will first explain what ToC is, then I will guide you so you can use every day.
The theory of constraints improves the performance of the entire value chain. Here are 5 steps to remember to apply it. Identify the bottleneck, decide how to best use this equipment or process, ensure new rules are followed, elevate the system’s constraints, if need be, start over on the new bottleneck.
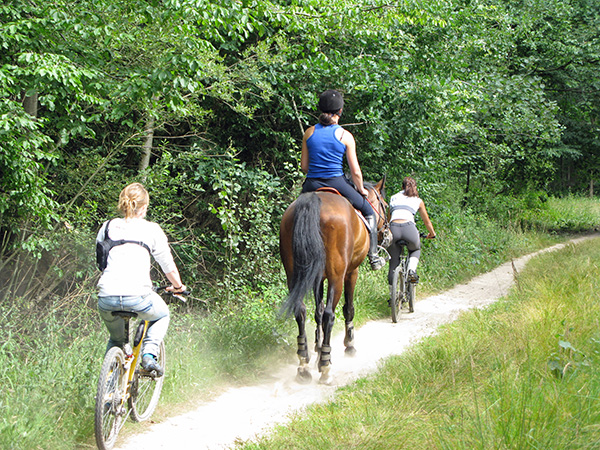
Principle of the Theory Of Constraints
Since the strength of a chain is determined by the weakest link, the first step to improving an organization must be to identify the weakest link.
Eliyahu M. Goldratt (1947 – 2011), Expert en gestion d’entreprise Israélien
Auteur de Le But : un processus de progrès permanent
The rhythm of the production line is conditioned by that of the slowest equipment. The theory of constraints helps to identify this equipment. By raising the system constraint, you optimize your production.
In his book, Goldratt gives several examples to illustrate the Theory Of Constraints. Besides the steel chain, and its weakest link, the troop of Scouts in the forest marked me very much.
Indeed, even if some young people are faster, the Scout troop will only arrive at the camp when all the Scouts have arrived. Even if they are not physically connected, it is the slowest that dictates the rhythm.
The performance of the troop depends on the proper use of resources. If the slowest one carries the heaviest bag, he will be even slower. If he has to keep up with the fastest, he will “overheat”. A stitch or shortness of breath would slow down the group even more.
By having everyone to stand on his slower pace, we preserve the resources. It is then possible to carry his bag for example, to speed up his pace and that of the team.
The rhythm of the production line, its takt time, is conditioned by that of the slowest equipment.
How to identify the bottleneck
Commonly referred to as a bottleneck, the constraint equipment is generally easy to identify. During a Gemba, you will quickly see where the accumulated stocks are. Take the time to observe the situation, because it is not always so obvious. Remember the story of the Hare and the Tortoise. Faster equipment may cause operators to take breaks or go elsewhere to help. The stock then accumulates at the entrance of the equipment, which is not bottleneck.
You can use a mapping such as VSM (Value Stream Mapping), with the working time on each equipment to help you. You can also ask the operators, who are often very aware of production bottlenecks. Routings can also guide you. In the end, what is important is that you are certain to address the equipment(s) that generate the constraints. We are talking about the weak links in your factory.
How to remove the bottleneck
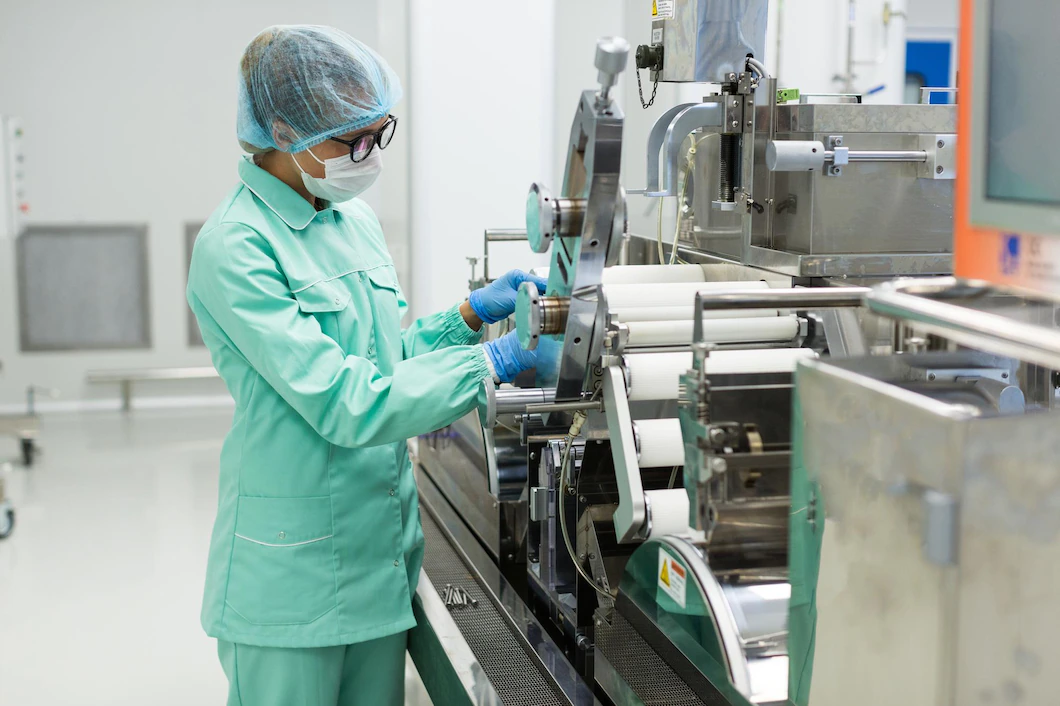
Then it is the time of observation. You need to determine why this equipment is causing a bottleneck. It is necessary to make a precise diagnosis in order to address root causes. Using several times the 5 Why, you will draw a causes tree. Then you can decide on the right plan of action.
Here are some examples of common causes:
- The equipment is not reliable. The operator must frequently make adjustments. She does a lot of checking of parts. She adjusts the machine during production. Or she reworks certain pieces twice to get them right. In this situation, it is the Six Sigma methodology that will help you reduce the variability in production.
- The equipment is long to prepare for each new series. You work with smaller batches, but this equipment takes time to set up. You have increased the batch sizes, but it does not meet the need. In this case, it is the SMED that will help reduce the time required to go from one type of part to another.
- The workstation is overall disorganized. The operator does a lot of manipulation. She moves the pieces several times, making numerous trips back and forth. In this case, you’ll have to start with a spaghetti diagram. You can then improve the flow and especially the ergonomics of the workstation. You may be reorganizing the teams or prioritization.
In any case, you will not forget to use the 5S to finalize your improvement workshop. It is usually with a Kaikaku approach that the bottleneck is corrected. A team works for a few days to solve the constraint.