Perseverance is about continuing your efforts.
Resilience is when you get up after falling down.
Grit is when you get up and keep on getting up.
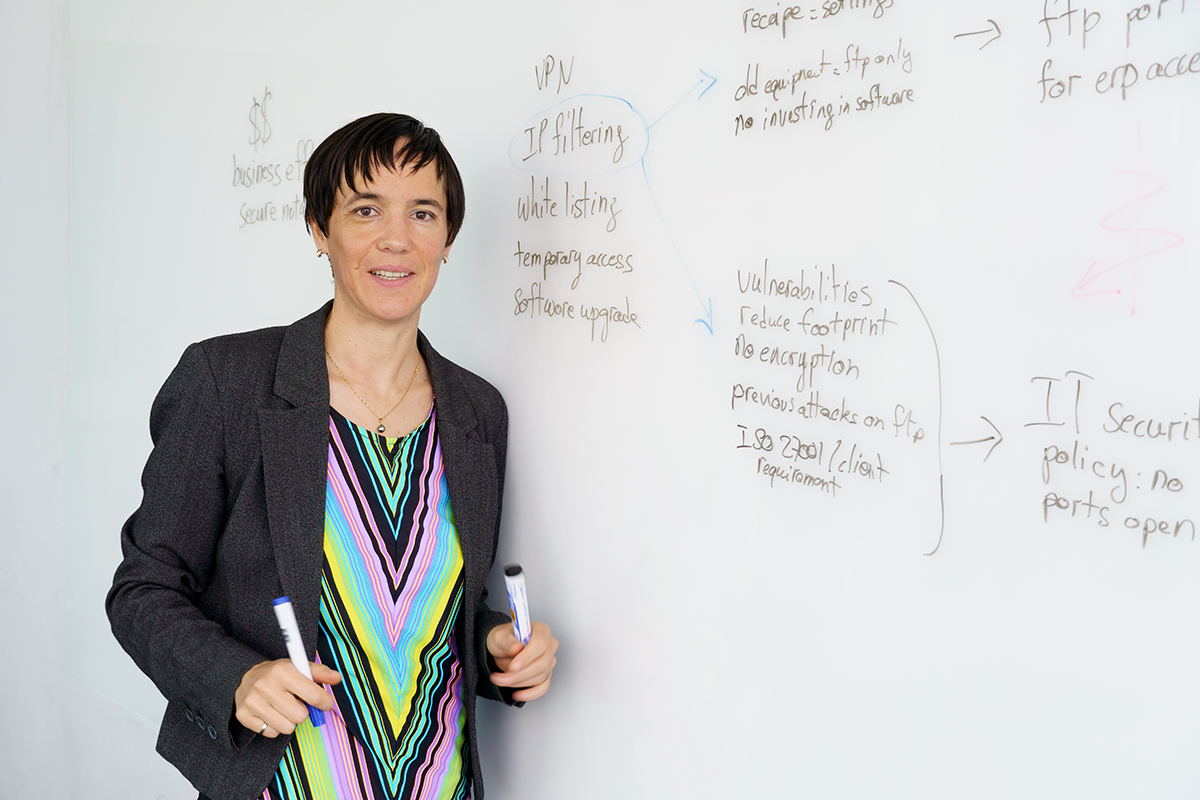
In a complex word (chaotic sometimes), it is human to feel a bit lost. I guide directors and presidents in critical moments: new role, organizational or technological changes …
With a profile combining operations to information technology, regulations to performance and strategy to projects, I am the best guide to make your organization thrive.
Quick question or big challenge, contact me for a free 30-minute consultation!
Empower yourself!
We can achieve all our projects and overcome any obstacles. We just need the right mindset, the right tools and the right support. With this website, I share tools and techniques to improve your ways since 2009.
Learn about Lean and Agile methodologies and tools. Discover my posts about leadership, change management and organizational strategy. Finally, take the time to understand how you work and your biases to elude these habits or preconceived thoughts.
Combining your efforts with time, you will achieve what once seemed impossible.
Technology at the service of performance.
I have always had an interest in technology. As a child, I wanted to become an IT engineer. Studying industrial engineering, I delved into programming, which I really enjoyed. The satisfaction of finding the last bug in my code was proportional to the time required to find it.
With my industrial engineering degree, I started my journey in factories. I obtained my first two certifications: Lean Bronze by the Society of Manufacturing Engineers (SME) and Green Belt Six Sigma by the American Society for Quality (ASQ). I consistently leveraged technology to simplify processes and increase efficiency. During my first consulting assignment, I developed an ERP in Access and VBA. Later, I implemented a scale-based solution to automate tiring manual counting procedures in the pharmaceutical industry. My understanding of Lean concepts and statistical skills were key to success in demanding environments.
During my professional journey, no problem has been too small for me to consider, nor too big for me to tackle. My curiosity combined with a rigorous scientific approach adapts to every problem’s size and type.
I’ve always strived to simplify, solve and improve.
My problem-solving approach
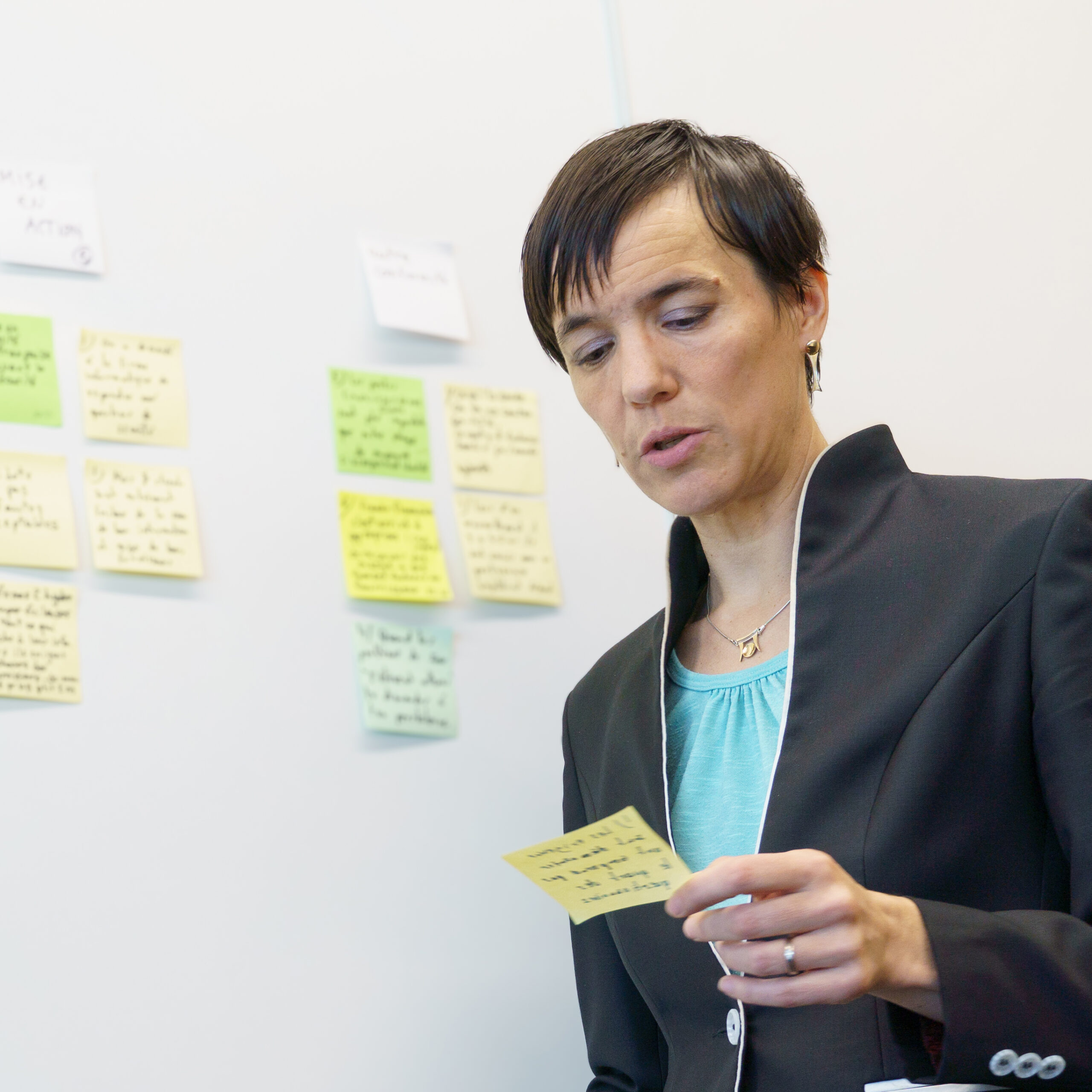
My working approach revolves around looking at the big picture, delving into details, and bringing opportunities to light. I’ve always favored an iterative approach. We start from the current state and slowly progress to our target. We get quicker gains and can adjust our plan to the changing environment.
This led to my Professional Scrum Master certification, which highlights my skills and experience in leadership roles ranging from project and product management to coaching and strategic planning.
But finding solutions is not enough, change only produces results when the whole organization embrace it. So I turn complex concepts into simple stories to engage everyone.
As an example, I created the first video training for 3000 insurance agents, as I recognized that a video format would make the new product easier to understand than just relying on words and pictures.
If a picture is worth a thousand words, a story evokes emotions that inspire action.
IT security, a base requirement to operate.
The digital age has ingrained computing into our daily lives, weaving a web of dependence that cybercriminals skillfully exploit for their own gains. Operations are disrupted, data stolen relentlessly, and targeted businesses suffer financial losses and customer desertions.
Faced with these challenges, I wanted to learn more so I could better support organizations. I am Certified in Cybersecurity by the International Information Systems Security Certification Consortium (ISC2) as well as a Certified Information Privacy Professional (CIPP/Canada) and Certified Information Privacy Technologist from the International Association of Privacy Professionals (IAPP).
Adding these skills to my operational knowledge, I bring CTO and CSO to prioritize based on operational impacts. I also support operations to understand IT limitations and leverage the most efficient and cost-effective solution to remain competitive.
My objective is clear: to equip small structures by offering them the means to control their digital security, one action at a time.
An entrepreneurial adventure.
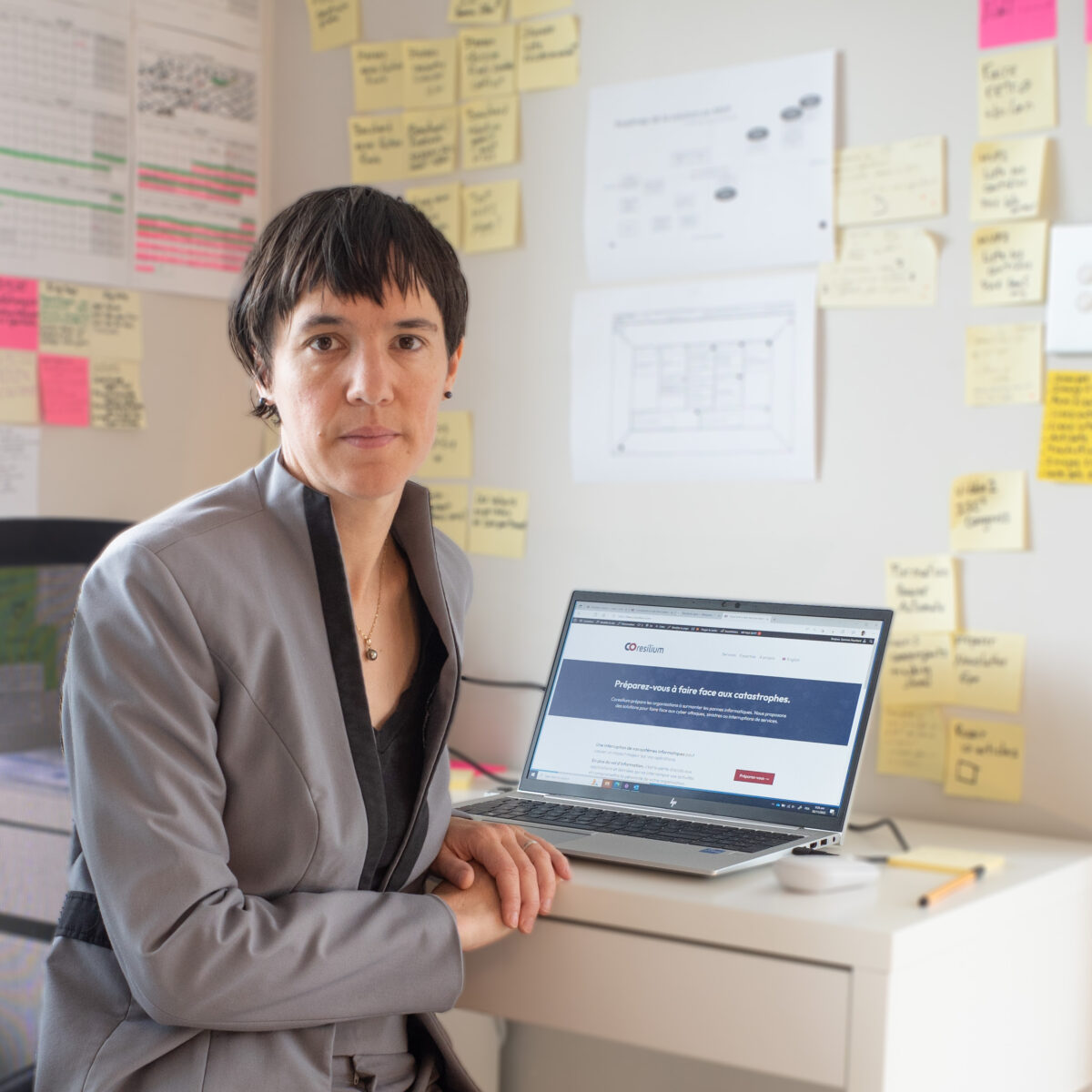
And since two challenges are better than one, I decided to start my own business.
With my experience in project management, organizational strategy and customer-oriented development, only the impostor syndrom was keeping me away from success. Indeed, I know how to provide value to my clients. Je sais aussi comment créer une organisation performante, j’ai tous les outils (ou presque) pour réaliser ma vision.
Today, Coresilium offers strategic and cybersecurity consulting on three continents. There is no challenge too big to overcome. To succeed, you have to try, learn and adjust. Every organization is different and I tailor solutions to your reality.
Find answers to your questions, book your 30-minute free consultation!