RPA… Robotic Process Automation. A new buzzword, a trend or an innovation to be more efficient? It is impossible to effectively automate a process that is not mastered.
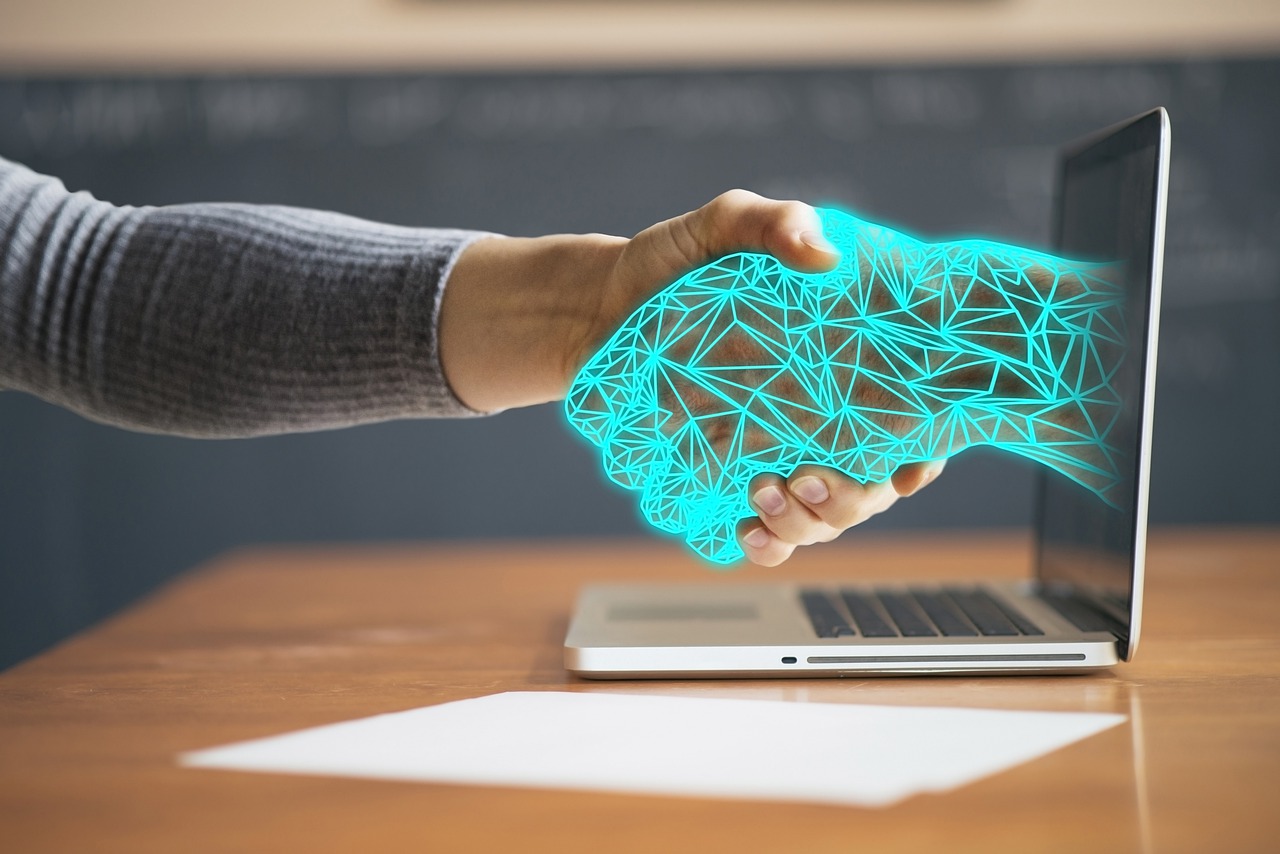
Various RPA platforms(IBM, Automation anywhere, NICE, Blue Prism)promise astronomical efficiencies with the addition of robots to your team. What’s really going on? Industrial robots have replaced many jobs and improved factory productivity. Will services (finally) become efficient thanks to robots?
Robots, what a great idea!
Let’s start with the benefits. A robot works all the time, doesn’t make a mistake, never gets tired. It does not develop tendonitis when it clicks between different screens. It doesn’t complain and never takes a break. In short, a perfect employee.
The robot is programmed, it executes a clearly defined process, in the same and repetitive way. This is typically the kind of activity that is boring, tiring or demotivating for teams. So it makes sense to replace them with robots.
Beware of false efficiencies
As I mentioned in an article on false efficiencies in air transportation,we must be vigilant. A waste-generating process will continue to generate waste after it has been automated. It will generate even more. A process that is useless and costs the organization, will continue to cost after automation. Robots are inexpensive resources, but not free either.
If your customers complain that your service is not efficient, automating to speed up is not always the answer. The problem is not necessarily the speed of execution. When looking to improve a process, or a result, you always have to look at the root causes.
Beware of false good ideas: satisfying a customer is solving her problem, correcting the source of the problem and not the symptom.
For example, if you cough and go to a doctor. He can simply treat the symptoms (cough) with honey infusions or syrup. If you have bacterial pneumonia, you will remain sick. This is why the doctor asks you several questions before making a diagnosis and choosing your treatment.
RPA: How to automate a process
The automation of processes with robots mainly concerns administrative processes. I suggest 5 steps to get the most out of your robots.
- Make a diagnosis using Theory of Constraints or identify the root cause of your problem with the 5 why or a cause-effect diagram.
- Choose the process to automate, with an evaluation grid. What is the type of data to process: hanwriting, printed paper, digital? How many systems and sectors or roles are involved in the process? How often does the process change, what is the volume of exceptions? How long are teams spending on the process right now.
- Mapping the process to make sure you understand it
- Address problems identified during mapping.
- Automate the process with a robot.