One of the basic tools for process improvement is mapping. It’s hard to get past. But what is the point of mapping? How to choose the right type of mapping? In this article, I go back to the basics and guide you in choosing the most appropriate tool.
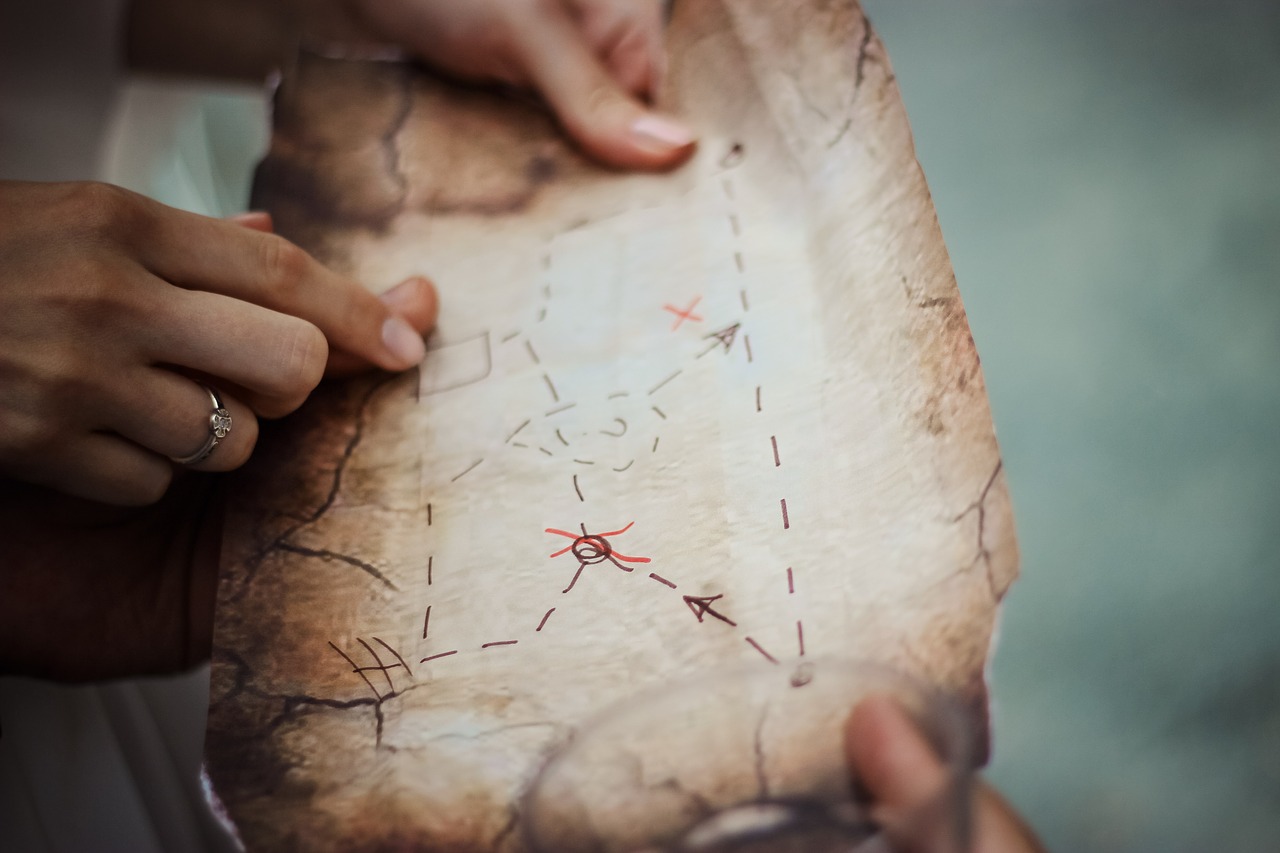
Why should you always start with a process mapping?
We’ve always used maps. This practice dates back to Antiquity and has proven itself. In process improvement, we use the same term, although the subject is a process rather than a place. The visual helps to understand the information.
A picture is worth a thousand words.
Confucius, philosophe 551-479 av J.C
More generally, a map is used to locate: where am I, what is the best path to get to my destination? With constantly updated maps, I’m always sure to take the right path. It’s the same with processes, by keeping the mapping up to date, the user always proceeds in the right way.
How do I use process mapping?
For me, mapping is primarily about starting a conversation. When a team draws a process, there are always surprises. It is from this conversation that improvements come from. By observing the process, it is easy to find ways to improve it. The nodes, the back and forth, the loops appear clearly on a map.
Ideally, mapping is done on the Gemba,or after a walk on the Gemba, so that everyone could visualize the process in action.
Mapping is then used as a reference document. It is used to train or execute processes. It’s the (living) memory of how the organization operates. The key processes of an organization should all be mapped. Imagine if only one person knows a region and resource supply area. If this person leaves the organization, you will need to explore the area again to rediscover the area. It is important to map and keep the most important knowledge up to date.
How to choose the right type of mapping?
The flow diagram
This is the easiest way to map a process. When I don’t know what kind of problems the process has, it’s the one I’m starting with. The nomenclature is simple: tasks are rectangles, decisions are diamonds and the whole thing is connected by arrows.
It also helps to identify the value chain.
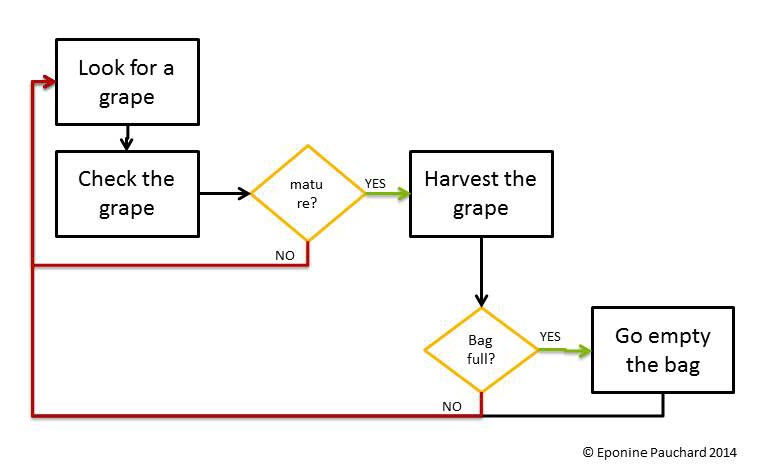
This mapping is useful for illustrating decision points or options. Being a functional diagram, it has no specific standard or requirement. However, I recommend keeping it simple. You can represent activities by rectangles, steps by arrows, and decisions by diamonds.
Value Stream Mapping
When you’re looking to improve timelines: cycle time, takt time or lead time,then you should use value chain mapping. The nomenclature is precise and requires training, but it is powerful. The bottlenecks are clear. It is also the tool of choice in the Theory of Constraints.
Documenting this type of mapping requires more research, as you will need to indicate times, defects, resources. The result is more complete and facilitates decision-making when improvements are not obvious. It is used in more mature organizations.
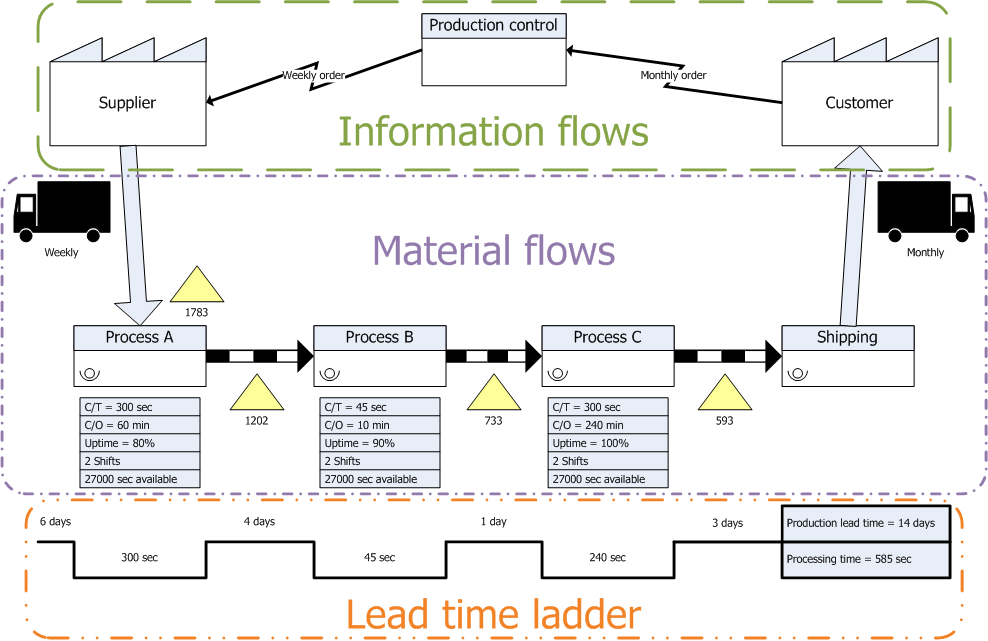
BPMN (Business Process Model and Notation)
This mapping takes the principles of the flow diagram, but adds an additional layer: swim lanes. These help to distinguish who does what. This is especially useful when trying to improve interactions between different departments, or to clarify roles and responsibilities.
For use as a technical diagram, to automate processes, you will have to be rigorous in the use of symbols and corridors. For the computer that interprets your diagram to understand it, it will be necessary to be precise and document all cases.
SIPOC
SIPOC (Supplier, Input, Process, Output, Customer) identifies processes by focusing on inputs and outputs. Its advantage is that it clearly identifies the interactions between the value chain and the outside. This is a good way to start if you are unsure of your main processes. It can be broken down into different levels of detail as needed.
It is also useful for defining the “sandboxes” or the limits of each process. Here is an example for the vineyard.
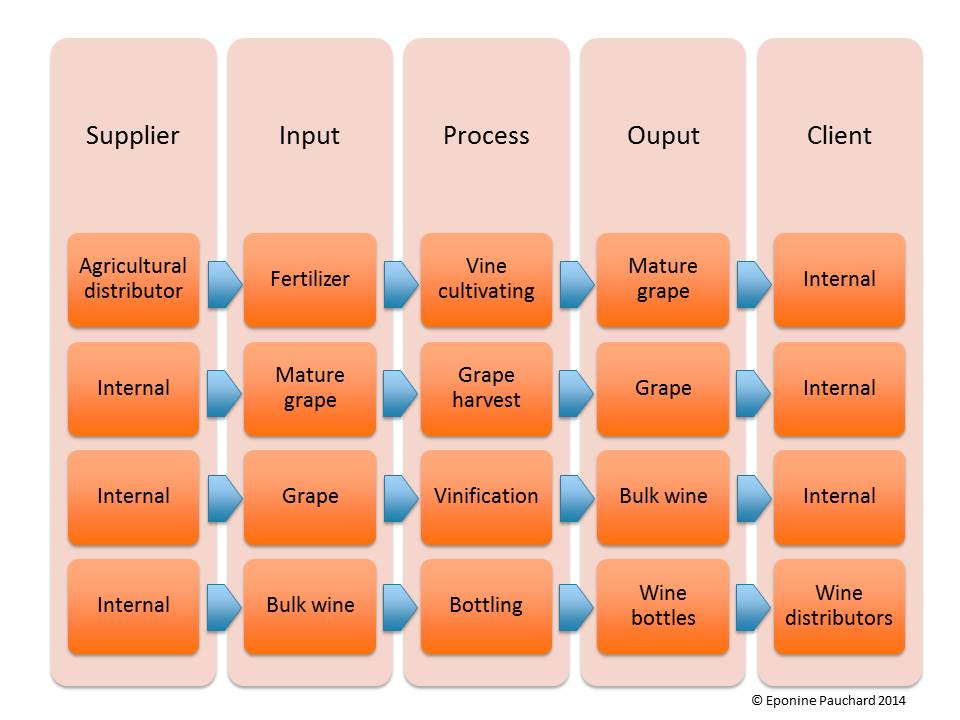
Service blueprinting
I’ve already shared a lot of details about this mapping. It aims to identify interactions between the client and the organization. The blueprinting service guides the improvement of the process on the customer’s efforts. It aims to simplify processes from its point of view.
When should you map a process?
All the time! Any improvement project should start with mapping, at least a draft, to ensure understanding. And preferably on Gemba…